Polyvinic Chloride, or PVC, is a kind of plastic you’ll find all over. It’s popular because it’s super flexible, lasts a long time, and doesn’t cost much to make. A part of making PVC that people sometimes don’t think about are the processing aids. These are like special helpers that make it easier to change raw PVC into the finished product.
Breaking Down PVC Processing Aids
Special additions mixed into PVC during production. Their job is to make the PVC stronger when it melts, help it blend better, and boost the end product’s quality. These helpers give the melting PVC more stretch and balance, which keeps the shape and structure of the final PVC products steady during production.
Types of PVC Processing Aids
There are several types of PVC processing aids, each with a unique function:
- Acrylic Processing Aids: The most common type used to promote PVC fusion, improve surface quality, and increase the processing speed.
- Lubricants: These reduce the friction between PVC molecules and the inner surface of the processing machine, preventing overheating and degradation of the PVC material.
- Impact Modifiers: These increase the toughness and durability of the PVC products, reducing their susceptibility to breakage.
The Role of PVC Processing Aids in the Industry
- Enhancing Product Quality: By improving melt strength and fusion, directly affect the quality of the end product. They aid in producing PVC products with a smoother finish, greater strength, and enhanced durability.
- Boosting Operational Efficiency: Processing aids contribute to increased production speed and higher throughput, crucial for maintaining operational efficiency. They also reduce energy consumption by lowering the processing temperature.
- Cost Savings: By extending the lifespan of machinery, reducing waste, and improving product quality, PVC processing aids can lead to substantial cost savings.
PVC Processing Aids: A Closer Look
They are a kind of polymer additive, usually based on acrylic polymers. Their main job is to make PVC easier to work with and perform better in many uses. They mainly work by helping PVC blend better, making it stronger when melted, improving its shine, and making it smoother. Let’s take a closer look at some common PVC processing aids.
- Acrylic Processing Aids: These are the most widely used processing aids in the PVC industry. Their main purpose is to promote fusion, ease melt flow, and improve the surface quality of PVC products. By integrating themselves into the PVC matrix during the fusion process, acrylic processing aids reduce the amount of energy needed to fuse the PVC. This not only increases processing speed but also improves the appearance and durability of the final product.
- Lubricants: Within the PVC process, two types of lubricants are used – external and internal. External lubricants like paraffin waxes and stearic acid derivatives create a film between the PVC and the metal surfaces of the machinery, minimizing friction and preventing the PVC from sticking to the machine. Internal lubricants, such as esters and amides, reduce friction between PVC molecules, reducing shear stress and heat generation during the processing phase.
- Impact Modifiers: These are used to enhance the impact strength of rigid PVC products, especially in applications where toughness is required, like in PVC pipes, doors, and window frames. Commonly used impact modifiers include Chlorinated Polyethylene (CPE), Acrylonitrile Butadiene Styrene (ABS), and Methacrylate-Butadiene-Styrene (MBS).
The Unseen Impact of PVC Processing Aids
They are key to making strong, lasting, and affordable PVC products. They make the manufacturing process smoother, cutting down on machine wear and halting production less often. By improving the look and toughness of PVC products, they directly increase customer happiness and help the products stand out in the market.
These aids also help the PVC industry become more eco-friendly. By allowing the use of lower heat during production, they decrease both power use and CO2 output. Plus, they enable more recycled materials to be used in making PVC, which supports a greener, more reusable economy.
They are essential in the plastics industry. They help create top-notch, long-lasting PVC products. By improving the quality of the products, making operations run smoother, and saving costs, they continue to be crucial for the industry’s ongoing growth and progress.
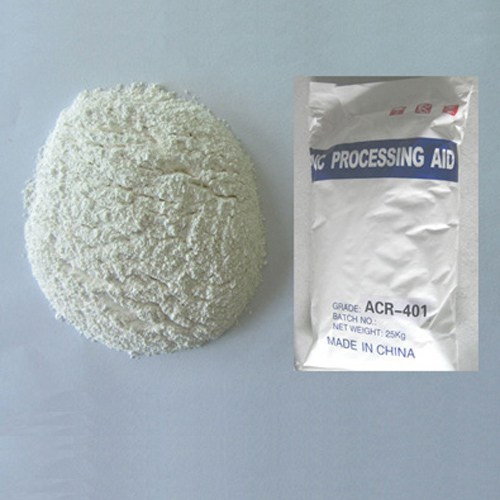