Calcium stearate is a crucial ingredient used in various industrial applications, such as plastic production, food manufacturing, and pharmaceuticals. Produced from stearic acid and calcium oxide, this waxy substance serves as a release agent, stabilizer, and surface conditioner. The need for calcium stearate in modern manufacturing highlights its significance. However, despite its ubiquitous nature, the process of making calcium stearate is not commonly understood. This article aims to break down the intricacies involved in the manufacturing process, key properties, and applications of calcium stearate.
Chemical Structure
Calcium stearate (Ca(C18H35O2)2) is a carboxylate, specifically an organic salt made by combining stearic acid and calcium oxide or calcium hydroxide. It is a white, waxy powder that is insoluble in water but soluble in oils and other organic solvents.
Key Properties
- Thermal Stability: Excellent for high-temperature processes
- Lubrication: Provides good lubricity in plastic production
- Non-toxic: Generally Recognized As Safe (GRAS) for food and pharmaceuticals
Raw Materials
- Stearic Acid: Derived from animal fats or palm oil.
- Calcium Oxide or Calcium Hydroxide: Obtained from limestone or quicklime.
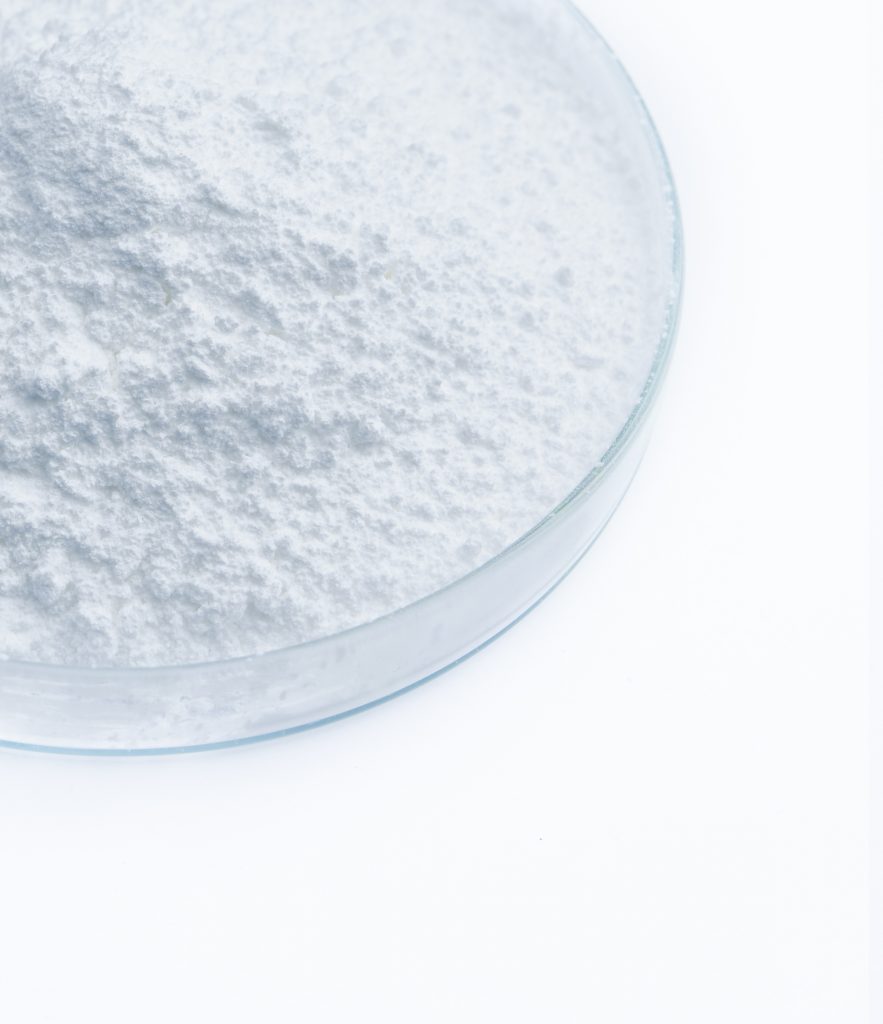
Manufacturing Process
1. Pre-treatment of Raw Materials
- Purification to remove impurities.
- Processed to a fine powder for better reactivity.
2. Mixing (Manufacturing Process of Calcium Stearate)
The stearic acid and calcium oxide are mixed in a reactor under controlled temperature and pressure conditions.
3. Reaction
The mixture reacts to form calcium stearate and water through a saponification process, which usually takes several hours.
4. Filtration & Separation (Manufacturing Process of Calcium Stearate)
Workers then separate the formed calcium stearate from the reaction mixture using filtration or centrifugation.
5. Drying
Then, workers dry the separated compound in an oven or with industrial dryers to eliminate any remaining moisture.
6. Grinding (Manufacturing Process of Calcium Stearate)
Then they grind the dried product into a fine powder.
7. Quality Control
Technicians take samples for testing to verify that the product meets specific industrial standards.
Applications (Manufacturing Process of Calcium Stearate)
1. Plastics Industry
Used as a stabilizer and a release agent in the production of PVC and other polymers.
2. Food Industry
Acts as an anti-caking agent in spices and baked goods.
3. Pharmaceuticals
Used in the production of tablets as a flow agent.
4. Cosmetics
Acts as a stabilizer in various skincare products.
5. Construction
Used in concrete mixtures to improve workability.
Environmental Impact & Safety Measures (Manufacturing Process of Calcium Stearate)
Certainly, manufacturers prioritize safety precautions and environmental controls as a matter of utmost importance. To this end, advanced filtration systems have been implemented. Additionally, chemical treatments are utilized not only to maintain safety standards but also to reduce emissions and waste effectively.
Market Trends
Due to the growing demand from various industries, there has been a significant push for innovations in the manufacturing process. Consequently, these advancements aim to increase efficiency and, furthermore, reduce costs.
Conclusion (Manufacturing Process of Calcium Stearate)
Understanding the manufacturing process of calcium stearate provides insights into its essential role across various industries. The advancements in its production process not only make it cost-effective but also environmentally friendly, thus sustaining its importance in modern manufacturing for years to come.
By diving deep into its manufacturing process, applications, and implications, one can better appreciate the complexities and utilities of this seemingly simple compound. Calcium stearate is more than just a white, waxy powder; it’s a cornerstone of modern manufacturing that affects our daily lives in countless ways.